AMR
Targets and Results
Medium- and long-term targets and results
Table 1: Discharge limits in the receiving environment for active pharmaceutical ingredients (APIs) of antimicrobials handled by the SHIONOGI Group and audited items (those in color were subject to audit until FY2023)
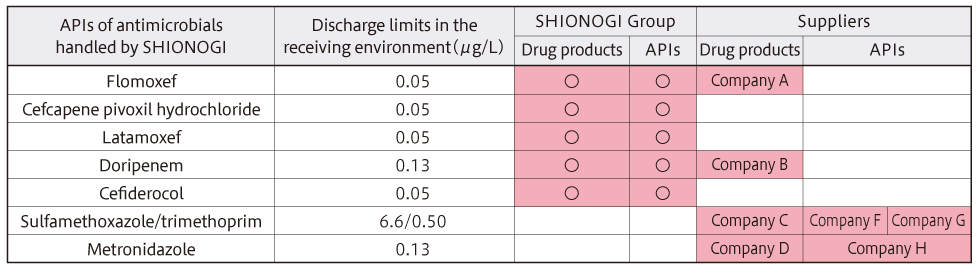
Although we had set a goal to maintain and improve the antimicrobial release management system at our plants and complete the initial AMR audit of all related suppliers by FY2024, we were able to complete the initial AMR audit of all suppliers in FY2023, achieving the goal one year ahead of schedule (Table 2).
All AMR audits at SHIONOGI, as mentioned above, are conducted based on the Antibiotic Manufacturing Standard*1 (“Standard”) stipulated by the AMR Industry Alliance (“AMRIA”),*2 ensuring that we have a system for controlling and managing the release of antimicrobials into the environment based on a global standard.
*1 Antibiotic Manufacturing Standard (External website)
*2 AMR Industry Alliance (External website)
We signed the AMR Industry Roadmap with 12 other leading companies and organizations at the World Economic Forum in Davos held in September 2016, thereby taking the lead in fighting with AMR. The signatory companies and organizations commit themselves to the strict management of antimicrobial release both by themselves and throughout their supply chains, through such measures as specifying their release management techniques in the form of a roadmap to be offered to all antimicrobial manufacturers so that they will also join in this worldwide effort to combat AMR. This movement has now developed into a major campaign called the “AMR Industry Alliance,” involving an increasing number of companies handling antimicrobials.
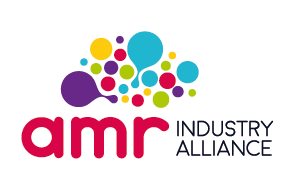
Table 2: Supplier audit results (by FY2023)
Supplier | Country of location | Management system | Wastewater management | Solid waste material management | Conformity to discharge limits |
---|---|---|---|---|---|
Company A | Japan | 〇 | 〇 | 〇 | 〇 |
Company B | Japan | 〇 | 〇 | 〇 | 〇 |
Company C | Japan | 〇 | 〇 | 〇 | 〇 |
Company D | Japan | △ | 〇 | 〇 | △ |
Company F | India | 〇 | 〇 | △ | 〇 |
Company G | India | 〇 | △ | 〇 | △ |
Company H | Italy | 〇 | 〇 | 〇 | 〇 |
○: Conforming to the “Standard”
△: Conforming to the “Standard,” except in a small number of aspects; remedial measures being implemented
×: Not fully conforming to the “Standard”; remedial measures being implemented
Figure: Summary of antimicrobials release control and management

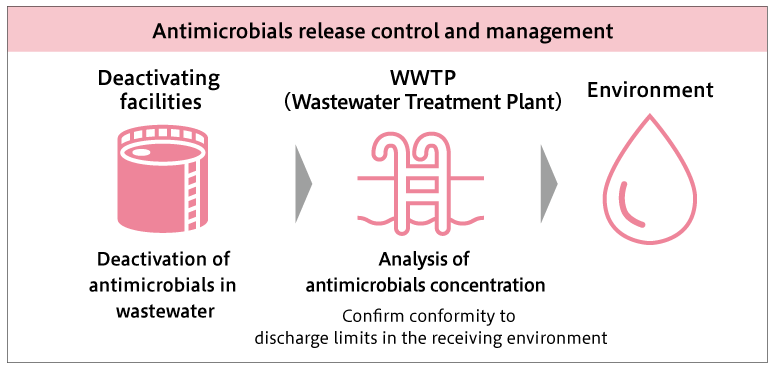
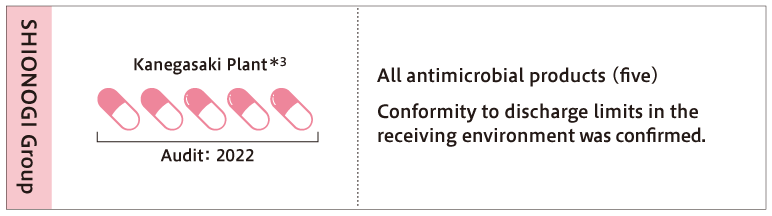
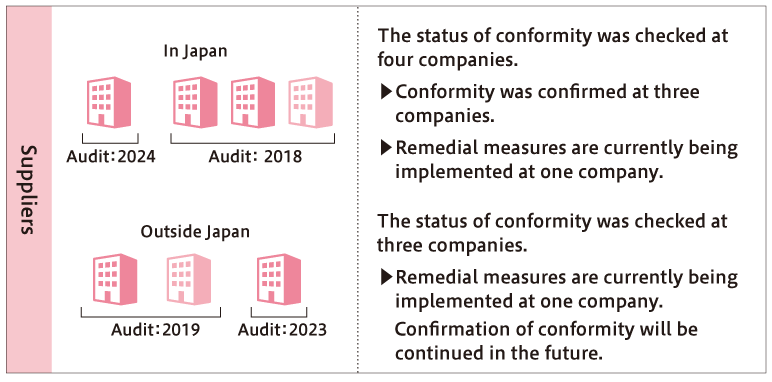
AMR Initiatives
Establishment of new medium- and long-term targets
The British Standards Institution (BSI) has announced a new international certification system called the "BSI Kitemark™ for Minimized Risk of Antimicrobial Resistance" in order to objectively evaluate and guarantee the minimization of antimicrobial resistance (AMR) risks in antibiotic manufacturing, based on the AMRIA Standard, in 2023. SHIONOGI conducts AMR audits based on the AMRIA Standard, but we also consider it important to obtain assurance that we are manufacturing antibiotics with responsibility and consideration for the occurrence of AMR, and to disclose this to our stakeholders. Therefore, as a specific response to our previous medium- to long-term goal of "achieving proper management of antibiotic environmental emissions throughout the supply chain," we have established a new goal for SHIONOGI in relation to AMR which is to have all antimicrobials provided by SHIONOGI are manufactured at plants certified by BSI, by the fiscal year 2035. In the fiscal year 2024, we have initiated planning and evaluating the feasibility of obtaining BSI certification for Cefiderocol, a multidrug-resistant gram-negative bacterial infection treatment.
Efforts to control and manage the release of antimicrobials
At Shionogi's flagship antimicrobial manufacturing plant, the Kanegasaki Plant, efforts to control and manage the discharge of antimicrobials include treating the wastewater produced during the manufacturing process with antimicrobial inactivation before being discharged through the on-site wastewater treatment facilities. Additionally, concentration analysis of antibiotics in the plant wastewater is conducted in accordance with the standards set by AMRIA. Currently, it has been confirmed that the concentration of antimicrobials in the wastewater from all five antimicrobial products manufactured at the Kanegasaki Plant is below the environmentally acceptable discharge criteria level*4, which means it has no impact when released into the natural environment. Furthermore, all solid waste discharged from the antimicrobial manufacturing process at the Kanegasaki Plant is collected and incinerated by an external contractor, ensuring that antimicrobials are not released into the environment as solid waste.
With regard to suppliers, we have confirmed that of the four antimicrobial products that we outsource the production of to domestic contractors, three products outsourced to three companies comply with environmental emission standards. We are currently implementing corrective measures for the remaining one product for which compliance has not been confirmed. Additionally, among the three antimicrobial products outsourced to three overseas suppliers, we have confirmed compliance with the environmental emission standards for two products outsourced to two companies. For the remaining one product where compliance could not be confirmed with overseas suppliers, corrective measures are currently being implemented. Moving forward, we plan to continue verifying the compliance status of the environmental emission standards for approximately 2-3 domestic suppliers and 1-2 overseas suppliers annually.
Participation in “One Health – AMR and the environment”
In June 2024, Mr. Gareth Morgan (Global Head, Portfolio Management and AMR Policy) of Shionogi Inc. participated as a panelist in the BSI-sponsored webinar event “One Health – AMR and the environment.” There, he explained to the audience, including antimicrobial manufacturers and suppliers, SHIONOGI’s efforts to control and manage the release of antimicrobials from its antimicrobial-manufacturing plants and the status of AMR audits of related suppliers.
“One Health – AMR and the environment” (External website)
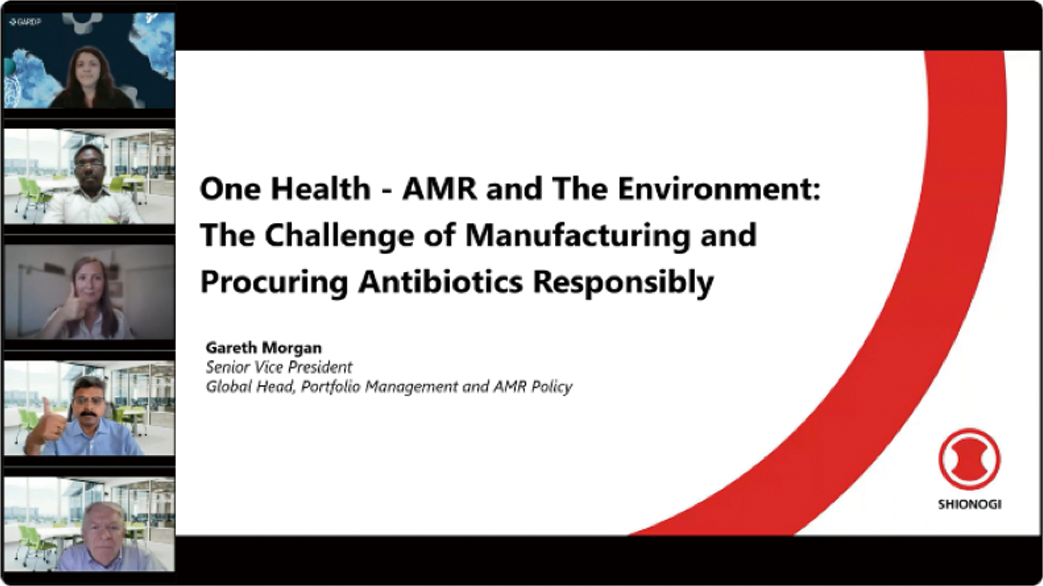