Environmental Governance
Environmental Governance Structure
To ensure business execution based on appropriate management judgment, the SHIONOGI Group (“SHIONOGI”) has opted to establish a company with a Board of Corporate Auditors. This is because it will enhance the auditing function of the corporate auditors and the monitoring function of the Internal Control Department, which has an internal auditing function, and promote the smooth functioning of the management monitoring system through cooperation between them.
See the section “Corporate Governance” for details.
SHIONOGI’s initiatives for the environment, health, and safety (“EHS”) are promoted in an integrated manner by each oparating site and Group companies under the leadership of the Corporate Officer in charge of EHS. The Senior Vice President, Sustainability Management Division has been appointed as the Corporate Officer in charge of EHS.
Chaired by the Corporate Officer in charge of EHS, the SHIONOGI Group Companywide EHS Committee comprises representatives from the group’s oparating site and presidents from Group companies, who are appointed as personnel in charge of EHS. The committee discusses Environmental Materiality, sets annual targets (EHS Action Targets) centered on each item of Environmental Materiality, and considers and checks the progress of plans and specific activities through management reviews, thereby promoting EHG activities. In addition, the Energy Conservation Committee, chaired by the Corporate Officer in charge of EHS and placed under the SHIONOGI Group Companywide EHS Committee, considers proposals for targets for energy conservation and global warming control, discusses specific measures to achieve climate change targets, manages their progress, and assesses compliance with laws and regulations.
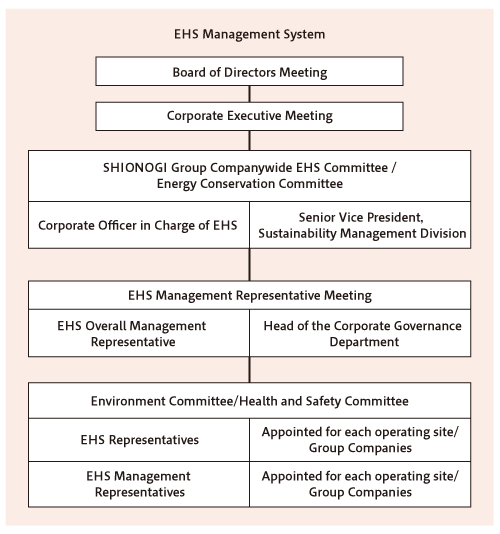
The operation of these two committees and the practical implementation of EHS activities in cooperation with the group’s operating sites are overseen by the EHS Group of the General Administration Department of SHIONOGI.
Among the matters discussed by the SHIONOGI Group Companywide EHS Committee and the Energy Conservation Committee, matters that have a particularly large impact on management are deliberated by the Corporate Executive Meeting and then decided by the Board of Directors. The committees also seek advice from the Board of Directors as necessary.
Environmental / Occupational Health and Safety Management Systems
ISO14001, ISO45001 certified business entities and initial registration
Settsu Plant |
Kanegasaki Plant |
Tokushima Plant |
Itami Plant |
|
---|---|---|---|---|
ISO 14001 |
Mar. 2021 |
Oct. 2022 |
Nov.2001 |
Apr. 2006 |
ISO 45001 |
Mar. 2018 |
Jul. 2015 |
Feb.2022 |
FY2025 |
Certification acquisition rate for factories (based on energy consumption)
Japan |
Global |
|
---|---|---|
ISO 14001 |
97.8% |
91.8% |
ISO 45001 |
89.9% |
84.5% |
Audits
ISO External audits |
Conducted by external accreditation organizations to verify that the group’s ISO 14001- and ISO 45001-certified management systems are operated in conformity with the standards |
---|---|
Internal Group audits |
A self-inspection within a company to verify the suitability and compliance of the system according to ISO 14001, ISO 45001, or our own management systems. |
EHS audits |
Conducted by the division that supervises SHIONOGI’s EHS initiatives, as directed by the management team. This is conducted separately from the internal group audits to ensure that EHS activities within the SHIONOGI Group are being properly implemented and maintained based on the management system, and that continuous improvements are being made. |
EHS audits of suppliers |
Audits of SHIONOGI’s suppliers of raw materials, intermediates, APIs, products, etc. conducted in compliance with the PSCI Principles |
AMR audits | Audits of the status of controlling and managing the release of antimicrobials into the environment from antimicrobial manufacturing facilities inside and outside SHIONOGI Conducted based on the Antibiotic Manufacturing Standard established by the AMR Industry Alliance See the section “AMR” for details. |
In addition to the above, for significant suppliers to SHIONOGI, we use EcoVadis, a rating platform for a fairer and more objective assessment of corporate social responsibility and sustainable procurement, to assess their fulfillment.
See the section “Supply Chain Management” for details.
Emergency Preparedness
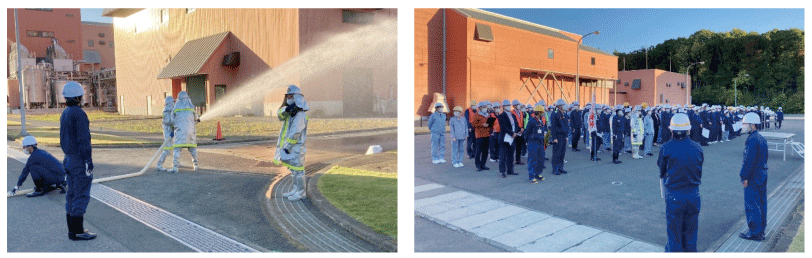